The Best End Of Lease Cleaning In Liverpool

Bond Back Guarantee

Friendly customer support

Professional, vetted bond cleaners
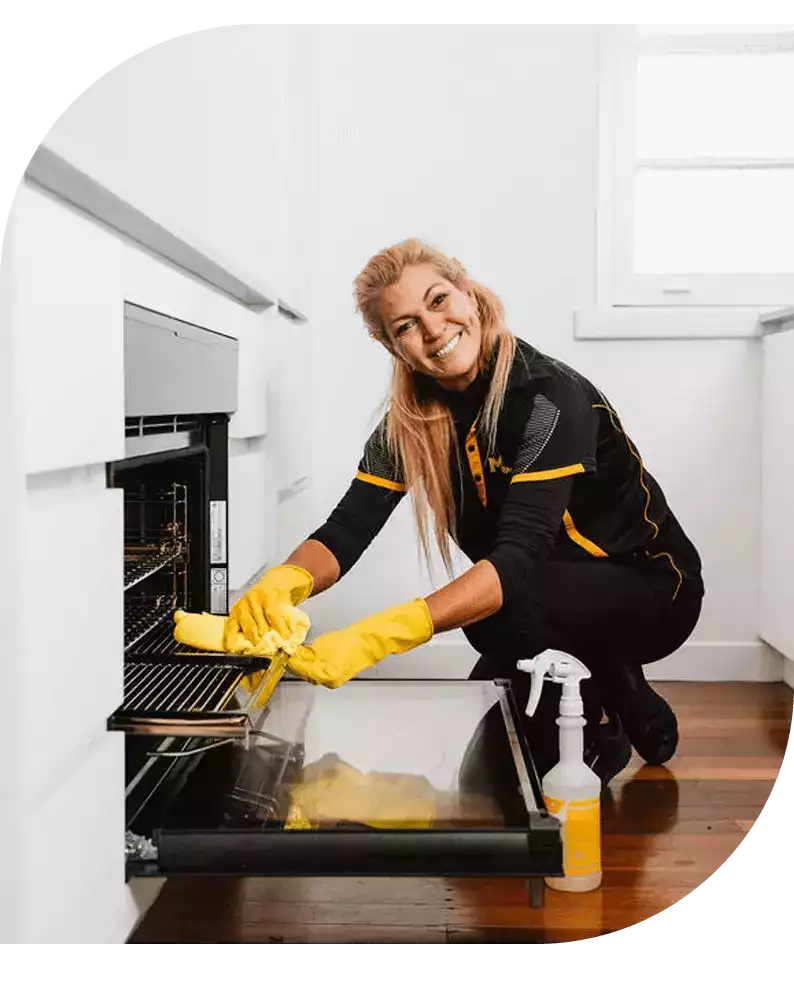
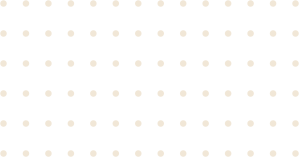
WHY MAID2MATCH?
More Than Just A Cleaning Service
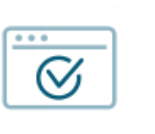
Easily book & pay online
Bond cleans are booked online with one simple process, using your phone or computer.
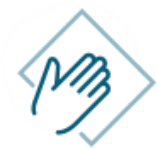
Expert end of lease cleaners
You can trust our cleaning teams to do the best job possible so you can get your bond back.
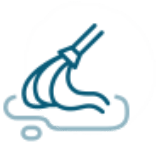
Cleaning equipment provided
For your convenience, our team brings their own cleaning equipment for each service.

Adaptable to your needs & preferences
Our cleaning teams are flexible and will accommodate your cleaning needs.

Convenient booking management
We’re just a message away for anything you need regarding your booking.

No lock in contracts for ongoing services
We don’t lock you into long-term contracts. Everything is in your control.
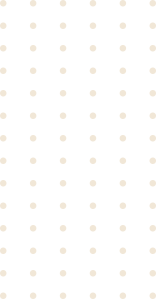
1800 207 686
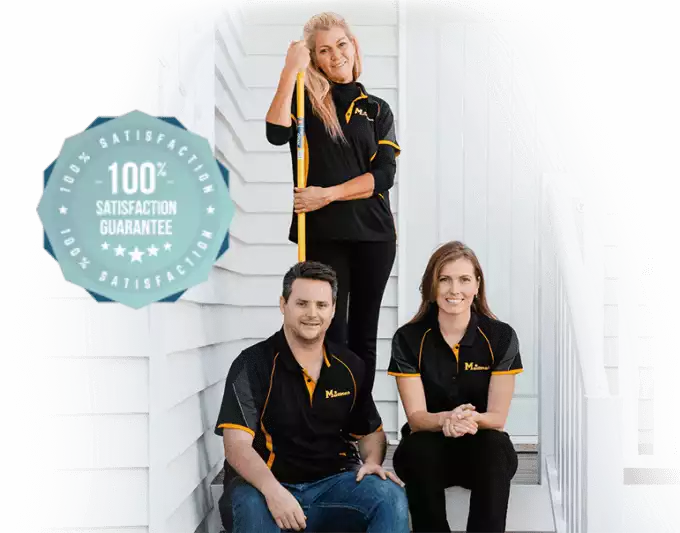
72 Hour Bond Back Guarantee
Maid2Match guarantees our end of lease cleaning will have your home looking better than when you moved in. If not, we’ll return within 72 hours of completion to fix any issues you or your real estate agent have — for free! If you or your property manager are still not satisfied, we’ll offer a refund on your booking.
WHAT'S INCLUDED
Maid2Match's Bond Cleaning Checklist
- Wipe down skirting boards
- Clean and dust lighting, switches and fixtures
- Vacuum and mop entryways and other hard surface floors
- Dust and remove cobwebs
- Wipe down inside and outside of doors
- Vacuum and mop floor
- Clean windows (internal), sills and tracks
- Wipe down skirting boards
- Clean and dust lighting, switches and fixtures
- Dust and remove cobwebs
- Clean sink and cupboards
- Wipe all counters
- Clean cabinets, cupboards, drawers and doors inside and out
- Clean oven inside/outside, cook top, grill and range hood (including filter)
- Clean dishwasher (internal, including filter)
- Clean and shine sink and taps
- Vacuum and mop floor
- Clean windows (internal), sills and tracks
- Dust and remove cobwebs
- Clean and dust lighting, switches and fixtures
- Wipe down skirting boards
- Damp wipe all kitchen bench tops

- Vacuum and mop floors
- Clean and descale shower screen and tiles
- Clean exhaust fans
- Clean bathroom sinks and bathtub
- Clean the toilet inside and outside
- Clean mirrors and wipe all counters
- Clean windows (internal), sills and tracks
- Wipe down skirting boards
- Clean and dust lighting, switches and fixtures
- Vacuum carpets
- Wipe down skirting boards
- Clean and dust lighting, switches & fixtures
- Dust and remove cobwebs
- Clean windows (internal), sills and tracks
- Spot clean walls
- Dust and clean fans
- Clean inside cupboards and built in wardrobes
- Clean windows (internal), sills and tracks
- Clean air conditioning unit filters (where removable)
- Wipe down skirting boards
- Clean and dust lighting, switches and fixtures
- Dust and remove cobwebs
- Vacuum and mop floor
- Dust and clean fans
- Spot clean walls Clean sliding doors inside/outside
- Garage: Vacuum/Sweep Out; clean and dust light and power points
- Front Door Area: Sweep
- Balcony or Verandah: Area cleared of spider webs/dust. Floors swept and cleaned with damp mop
These are not included in our standard bond cleaning service and need to be added as Extras
- Blind Cleaning
- Full Wall Washing
- Yard & Garden Maintenance through our partners Lawn.com.au (subject to location)
- Carpet Steam Cleaning (subject to location)
OUR TEAM
Local End Of Lease Cleaners In Liverpool
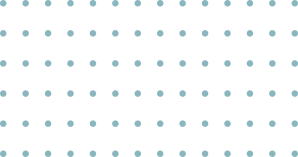
Lorena
Maid2Match Professional
Brigitte
Maid2Match Professional
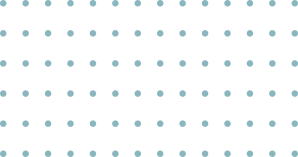
Nikita
Maid2Match Professional
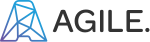
Your home is safely insured with us
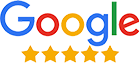
400+ FIVE STAR REVIEWS ON GOOGLE
FREQUENTLY ASKED QUESTIONS
Liverpool End Of Lease Cleaning Information
How much does end of lease cleaning cost?
We will give you an initial quote based on the number of bedrooms and your house size, and the amount of time we estimate it will take us to perform all the tasks on our bond cleaning checklist. If you request extra services, that will add extra cost. Our quotes vary from property to property, so contact us via our easy online form and get a quote today!
What is included in a bond cleaning service?
We have an extensive bond cleaning checklist that covers everything your real estate agent or property manager will look for. Our services will range from dusting and sweeping, to oven and window wiping, to bathroom cleaning. Our cleaners will also use their own eco-friendly equipment. If you require additional services, let us know!
Your Maid2Match cleaning team will ensure you get your bond deposit back with our end of lease cleaning, guaranteed 72 hours after completion.
How do I book a bond cleaning?
Access our easy online booking form on your mobile, tablet, or desktop to book a bond cleaning today — in less than a minute! Or call us to get a free quote and book your bond cleaning over the phone with our friendly team.
How long will the cleaning take?
A thorough and quality bond cleaning takes time! The number of hours will depend on the number of rooms and the size of your home. Contact us for your quote and estimate through our online form. Once your service is scheduled, our professional bond cleaners will then work efficiently while covering all areas as listed in our bond cleaning checklist. Moreover, our services are guaranteed for 72 hours after completion.
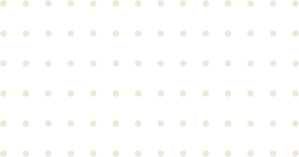
Does my house have to be empty?
Our cleaners can perform a bond clean most efficiently when all areas of the property are empty. Only leave furniture and other items if they belong to the property.
Do I have to be there during the service?
Not at all! You can feel safe and secure with Maid2Match handling your home. Just leave the key for our cleaning team to gain entry, and they’ll take it from there — only exiting your home when it’s spotless. Simply inform us of the key location ahead of your schedule. We’ll put it right back after!
Do you require the electricity to be on?
Our end of lease cleaning teams will need electricity and warm water to complete a thorough job.
What if I am not satisfied with the results?
Our end of lease cleaning services come with a guarantee you’ll get your bond back 72 hours after completion. If your estate agent or property manager finds anything amiss, our team will return to fix things up free of charge. So don’t worry — we’ll have your home looking better than when you moved in!
LOCAL END OF LEASE CLEANING
Other Locations We Service Near You
Sydney Suburbs
- Arncliffe
- Ashfield
- Auburn
- Bankstown
- Blacktown
- Bondi Beach
- Botany
- Burwood
- Cammeray
- Campsie
- Concord West
- Cremorne
- Crows Nest
- Darlinghurst
- Earlwood
- Erskineville
- Gladesville
- Greenacre
- Homebush
- Hornsby
- Hunters Hill
- Hurstville
- Kingsford
- Lidcombe
- Liverpool
- Manly
- Marrickville
- Mascot
- Neutral Bay
- Newtown
- North Sydney
- Parramatta
- Penrith
- Port Botany
- Randwick
- Rhodes
- Rockdale
- Rose Bay
- Rosebery
- Ryde
- South Coogee
- St Leonards